The threat of static electricity is sometimes hidden in the process of inkjet printing, which not only affects the printing quality and output effect but also threatens the safety of the equipment itself. As one of the leading technologies of digital printing, the performance of inkjet printing is constantly improving and the scope of application is constantly expanding. However, a small amount of static electricity always brings big problems, such as Printing ink splash.
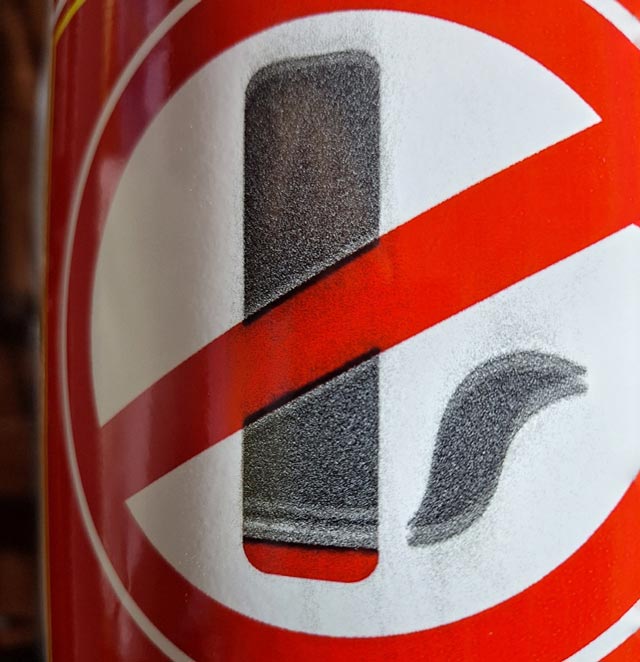
The Static Electricity
- Print Heads
Static electricity can cause dust and other minute impurities to accumulate inside the print head. These contaminants may lead to clogs, adversely affecting print quality, and, in severe cases, can damage the print head. - Ink
Static electricity can disrupt the ink during the ejection process, causing droplets to miss their intended landing points. This results in issues like missing drops, spots, blurriness, and smudging, not only compromising print quality and accuracy but also risking contamination of the internal components of the equipment. - Printing Media
Static can also cause the printing media (such as paper) to stick together during transit, leading to misalignment or paper jams. - Circuit Boards
Sensitive electronic components can be damaged by static electricity, resulting in equipment malfunctions, operational halts, or diminished performance. - Finished Product Quality
Static can attract dust and other particles, leaving the surface of printed materials unclean, such as Printing ink splash, which reduces product quality.
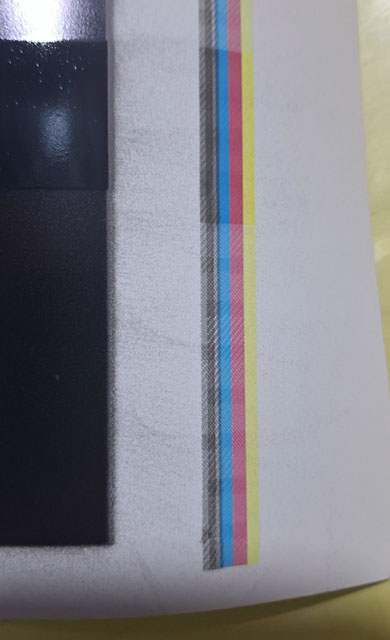
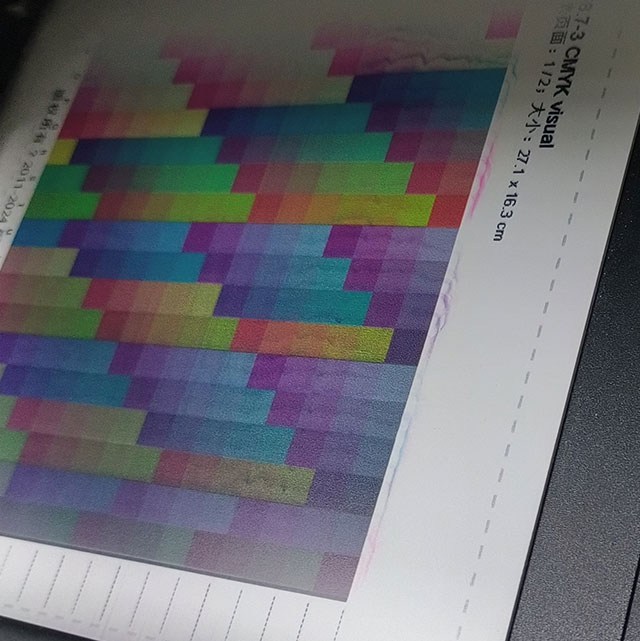
Causes:
Generally, materials possess an equal number of positive and negative charges that neutralize each other, preventing any display of electric charge. When external electrons are added, a negative charge occurs; conversely, the loss of electrons results in a positive charge. Both scenarios generate static electricity.
Common causes pertinent to printing include:
- Friction: Generated during the rapid movement of the printing media.
- Flow: Static can build up as materials move past each other.
- Separation: When materials are pulled apart, the charge can build up.
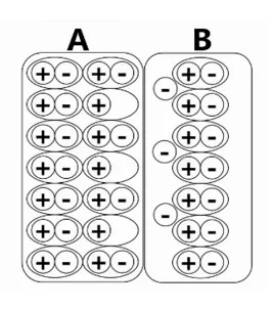
Factors contributing to static generation can stem from the printing equipment, the printing media, environmental conditions, and improper handling by personnel. For example:
- Areas containing electrical circuits without adequate insulation can easily generate static.
- High-speed friction between printing media can produce varying levels of static electricity.
- Weather significantly influences static formation; dryer conditions, particularly in autumn and winter, exacerbate static issues. Conversely, during thunderstorms, increased ionization in humid southern climates can also result in heightened static.
- Improper operator practices, such as neglecting circuit configurations or failing to monitor environmental humidity, contribute to static risks.
Solutions to threat of static electricity
- Installing Static Elimination Devices
Some advanced inkjet printing machines are equipped with static elimination devices, such as ionizing bars, which use high-voltage electrical fields to neutralize static charge on objects.
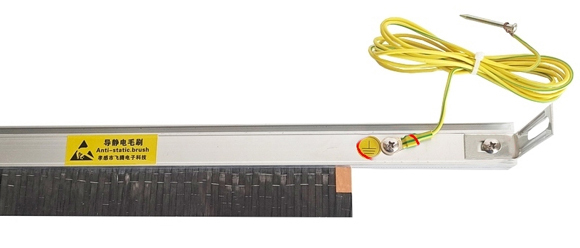
- Using Anti-Static Printing Media
Selecting printing media that has been treated to be anti-static, like specialized anti-static paper, can greatly mitigate the influence of static on the printing process. - Controlling Environmental Humidity
Maintaining optimal humidity levels (40%-60% relative humidity) can significantly reduce static generation; in such conditions, static charge levels can drop by up to 80%. This not only aids in achieving high-quality prints but also benefits the storage and handling of printing materials.
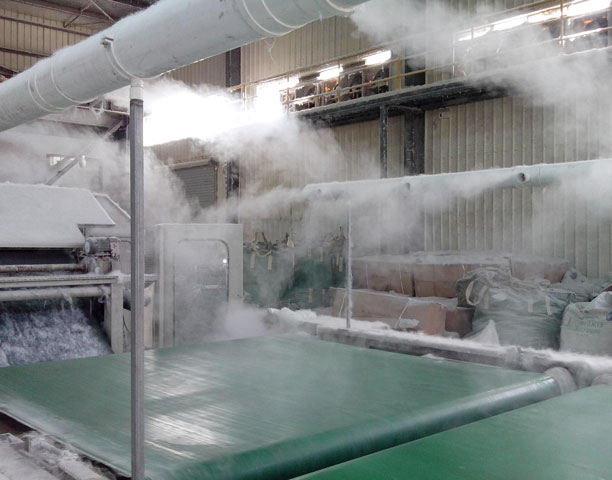
- Grounding Methods
Properly addressing grounding issues is crucial. A continuous, uninterrupted ground line should be established to prevent static accumulation, ensuring reliable contact with the machine. - Regular Cleaning and Maintenance
Regularly cleaning the internal components of the inkjet printing equipment, with particular attention to the print heads, helps prevent the accumulation of dust and impurities that can exacerbate static issues.
These measures should be tailored and optimized according to the specific model of inkjet printing equipment and its operating environment.
In addition to technical solutions, it is imperative to enhance employee training. Workers should fully grasp the dangers of static electricity and the corresponding preventive measures, ensuring that correct operational practices are maintained to reduce static accumulation in daily workflow.
More FAQ Articles.