There are three relatively mature processes for printing on cotton: reactive ink printing, DTF ink heat transfer ink printing, and DTG paint direct printing. Reactive printing is often used for large-scale roll fabrics, while DTF ink heat transfer printing and DTG paint direct printing are often used for T-shirt garment printing.
Mature processes for printing using Reactive ink:
Reactive ink has the best effect, with beautiful and bright colors and strong color fastness, without affecting the original feel of the fabric. Its disadvantage is that the process is extremely complex and the investment is large. It requires sizing-drying-printing-steaming-washing-drying, a series of complex processes, because sizing, steaming, and washing all require water, which pollutes the water a lot. The investment is also very large and is not suitable for small-format and small-scale printing. The best fabric printing effect currently on the market is the reactive ink process. But if you want to be cheap, easy to obtain, and effective enough, there is no complete solution yet. DTF ink heat transfer printing is a relatively cheap solution.
ITMA Exhibition-Reactive Ink Printing
Mature processes for printing using DTF ink:
DTF ink heat transfer printing comes from the improvement of the DTG paint direct printing process. DTG has appeared in this industry for many years, but it has always had a shortcoming. The color fastness is not good and it is easy to be washed off. The ink cannot stick to the material and the color will appear dull. In order to improve the shortcomings of DTG since 2020, the industry has produced DTF ink, which is printed on a coated film, and then uses hot melt powder to combine the ink and the fabric. The essence of the hot melt powder is a glue, use hot melt powder to stick the ink layer on the film to the clothes, and the color will appear. The DTF process solves the problems of color fastness and vividness, but another problem arises, that is, the hot melt adhesive powder will form a thick film, which is not breathable and feels very thick. Moreover, this film is on the surface of the clothes and will crack and fall off after a long period of scrubbing. It is also these shortcomings that make the DTF printing process only applicable in the mid-to-low-end fabric printing market. Within 1-2 years, the DTF printing process has rapidly spread in the mid- to low-end T-shirt printing market and has been widely accepted.
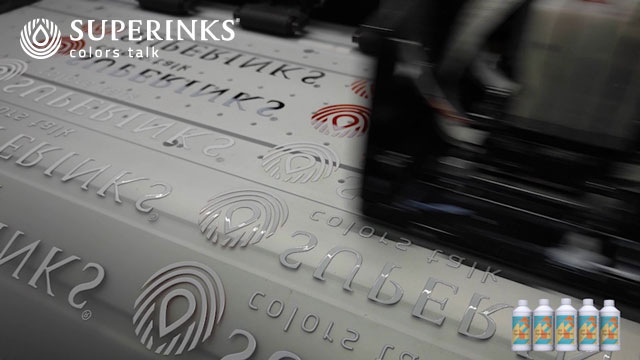
In the process of large-scale sales of DTF ink, the supporting products of the entire industry have been improved, and the cost of ink and resin has become cheaper; the stability and adhesion of the resin have also been improved, so the quality of DTF ink has been improved grade. DTG and DTF inks are 80% similar. On this basis, it has also led to the improvement of the entire industrial support for DTG ink. In addition, the slurry technology of the direct printing process of paint has also been improved in recent years, which has improved the direct printing printing of paint effect.
Mature processes for printing using DTG ink:
If you ask industry foresights about their views on the fabric printing industry, most people will say: DTG coating direct-printing printing on roll fabric is the future direction. DTG process sequence: ① first apply pre-treatment coating on the fabric, ② dry the coating, ③ print, ④ heat to fix the color. This process is just pigmented DTG ink printed on cotton material. DTG’s current pre-treatment liquid coating has also been improved. If you coat light-colored or white fabrics and use DTG direct spray, the printing effect can basically be accepted by the current market and industry; dark fabrics use DTG technology, bright colors The strength and color fastness still need to be improved. The reason is that when processing dark fabrics, if the pre-treatment liquid is thick enough or heavy enough, the entire fabric will become very thick, affecting the breathability and feel. If you make it too light, the ink’s carrying capacity will not be enough. Especially if you need to apply a layer of white ink on the fabric and then print a color picture on top of the white ink, the adhesion between the ink layer and the cotton fabric will be very weak. This is an area that needs to be improved.
Another pain point of the DTG coating direct spray process is: sizing, drying, printing, and drying. This requires at least two sets of equipment and two transfers of materials. It requires a lot of equipment, takes a long time, and requires a lot of labor.
A new idea!
Can a series of processes including sizing, drying, printing, and drying be operated on one machine and formed in one go? Reduce equipment costs, improve work efficiency, reduce labor costs, and of course improve print quality.
Nowadays, the commonly used nozzles in the DTG paint direct-printing process are: Kyocera industrial heads, Epson i3200-a1 photo heads, etc. The nozzles of these nozzles are 1-5PL, small nozzles, suitable for high-precision printing. However, such a nozzle is not suitable for slurry printing. The slurry from direct spraying of DTG paint is viscous and needs to be thoroughly soaked into the entire fabric. The nozzle for printing slurry needs a large PL, such as XAAR 128 80PL, or Spectra Nova 128 80PL. At this time, control board technology has made it possible for a set of boards in a printer to control two types of nozzles at the same time. In this case, you can only apply sizing to the part of the fabric where the picture is printed, saving sizing and less affecting the original feel of the fabric.
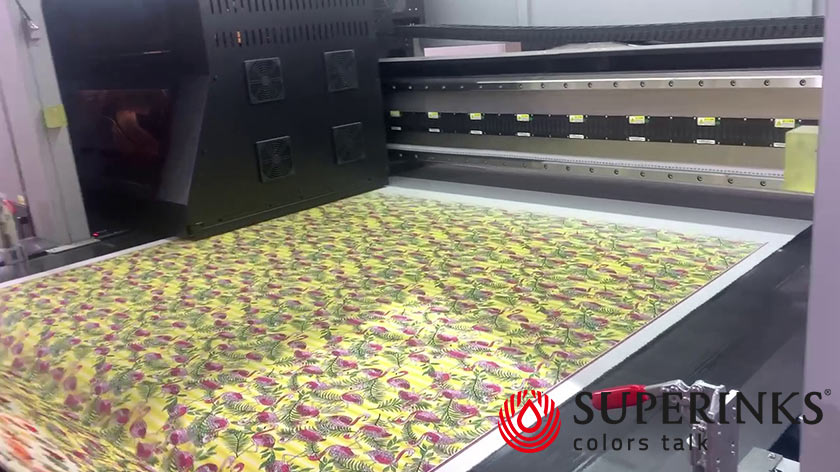
We saw HOMER(弘美数码), HPRT(汉印), HIINK(海印数码), etc. demonstrating this process at the ITMA Asia 2023 Shanghai exhibition. We look forward to receiving their samples and verifying the color fastness.
This idea is not only suitable for DTG printing, but also for dye-sublimation direct-printing, and even dtf-uv printing.
In the future, one type of printing head will print coatings or glue, and another type of high-precision printing head will print ink. If such a printer model is mature enough, it will be a printing model that saves energy and materials while ensuring quality.